Sculpture Workshop - Moulds
- carldurban
- Oct 19, 2020
- 5 min read
Updated: Feb 11, 2021
This workshop was a game of two halves. The mould part is to understand the process of making a piece-mould with a view to making multiple casts from a master. As part of the process it is also to understand which is the original and how multiple versions and duplicity takes away any uniqueness.
The actual pieces we made were not necessarily as important as understanding the process, the limitations and any issues that may arise from this process. We used plasticine to make objects that we could take the mould from in plaster. I looked to see what forms I could make and see how the material would react. It wasn't very pliable, so required a lot of manipulation and working. I made x4 objects, trying different shapes and textures to explore the limitations of the process. Even one of the simple shapes caused issues in finding the way to split the mould into x2 pieces. Two of the shapes I had to make into as three-part moulds.
The next part and most crucial part was to actually take moulds of the pieces. As I have done this before with direct casting the process was similar but this time is was the complete object not just one face. This meant working out how to do this to make sure no areas had an undercut and wouldn't 'pinch' when opened. The simple shapes I could make out just the two by trying to find a centre line along the shape that would mean the mould would open easily. Two of the moulds needed three part moulds, which meant dividing the shape into three. You can also take this onto further moulds if it needs it. It did mean that consideration of the original for this process has to be carefully considered.
Note the walls created to retain the poured plaster and the registration marks to ensure consistent duplication. Even the simple shapes created pinch points, which potentially will cause issues when the mould is poured. We also needed to add a 'sausage' which will allow entry for the mould to be poured. We are using wax in this instance, just to give an idea of how the process works. I am interested to see how this works and then also explore other mould making, using silicon and latex. I need to create some ideas and do the relevant research to explore the possibilities.
These negative piece-moulds are interesting in their own right. Because of the material used, Herculite Plaster, they have a bone like look and feel, almost fossil like. All the marks are transferred and in some ways the flaws of the original shape are magnified. It also highlights any issues of undercut or pinch-points, some of which can be modified at this stage. The actual shape of the various pieces isn't something you consider when creating them, you are purely looking at how to contain the plaster for the mould, the outer shape just happens, this could be controlled if you wanted to and could almost make these more interesting in themselves. Should they be rigid brick like rectangles or smooth stone shapes, that open like to expose the mould within, as if you have discovered a fossil.
Next stage, the pour...
Due to all the Covid stuff going on the actual pour had to be done by the NUA 3D Department. Missing this stage is a little frustrating but we were left the moulds to break open to see the wax mould inside. This process really informed me further as to what shapes worked and what struggled, even those I thought that would be easy to open, especially the three part moulds. Two out of the four really pinched, were quite stuck and needed a little help to release, this means the moulds would need modifying further prior to doing any further pours.

Having examine the pieces and moulds I have decided to take one particular piece and see if I can get a bronze cast of it. It is a shape that doesn't necessarily have a top, bottom, front or back. I just like the feel of it and the way it resembles a clasp or a connection between two pieces even though it is just one. It intrigues me as to how it will cast and feel when made of bronze.
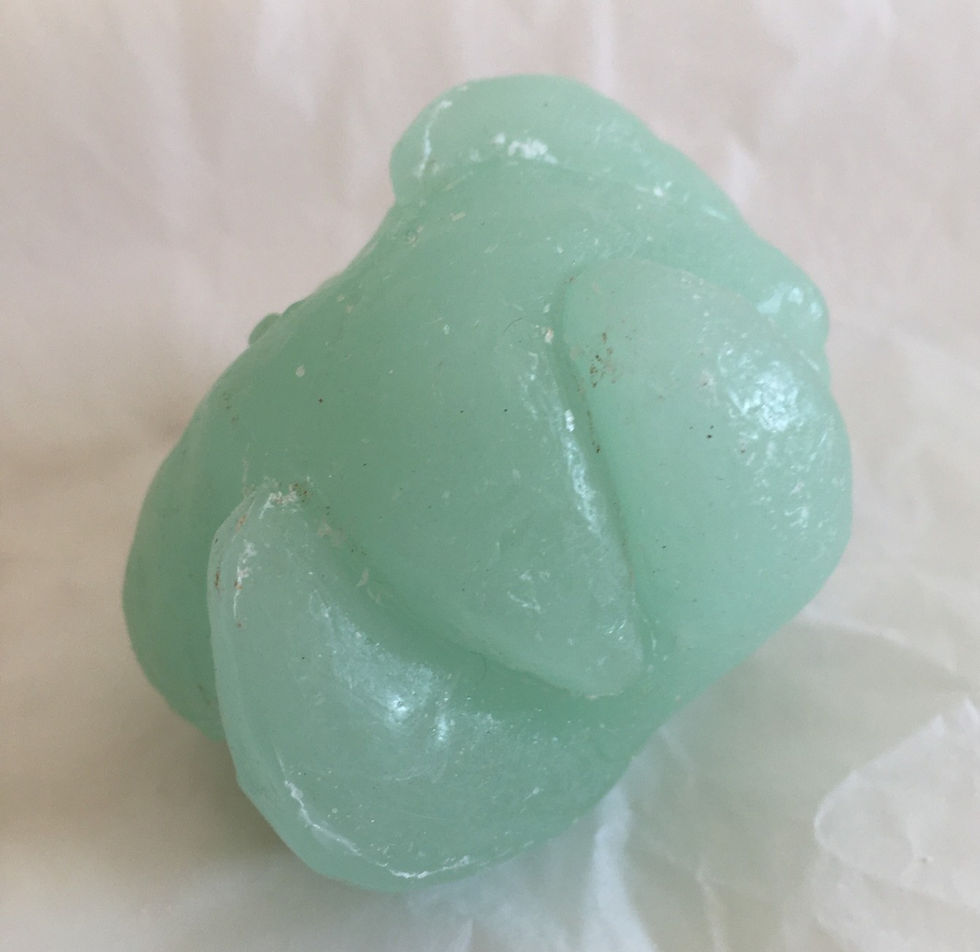
The other shapes all have merit and each one I created differently, using varying methods to shape and mark but the clasp one I feel needs further investigation.
Once all the moulds were opened and the casting 'shells' put together as a group it created some engaging images. The discarded fruit of the moulds fresh and shiny leaving their dried up husks.
Get in close the shells though and the original marks made in the plasticine are clearly visible along with the registration marks and the marks made by my hands and the tools I used to create them. The transference of these marks showing how everything is picked up in this process. It will be very fascinating to see how much this translates to the bronze version.
Making a bronze piece
I have never taken on any of my pieces to bronze and so wanted to experience the process in order to be able to create pieces in the future knowing how I could get them cast. In order to make the selected piece I had to 'run it up' using wax with sprues and an upturned paper cup, this that will be used to pour the bronze in and the sprues will become vents to let the gasses out, this was all connected using more wax and hot knives.
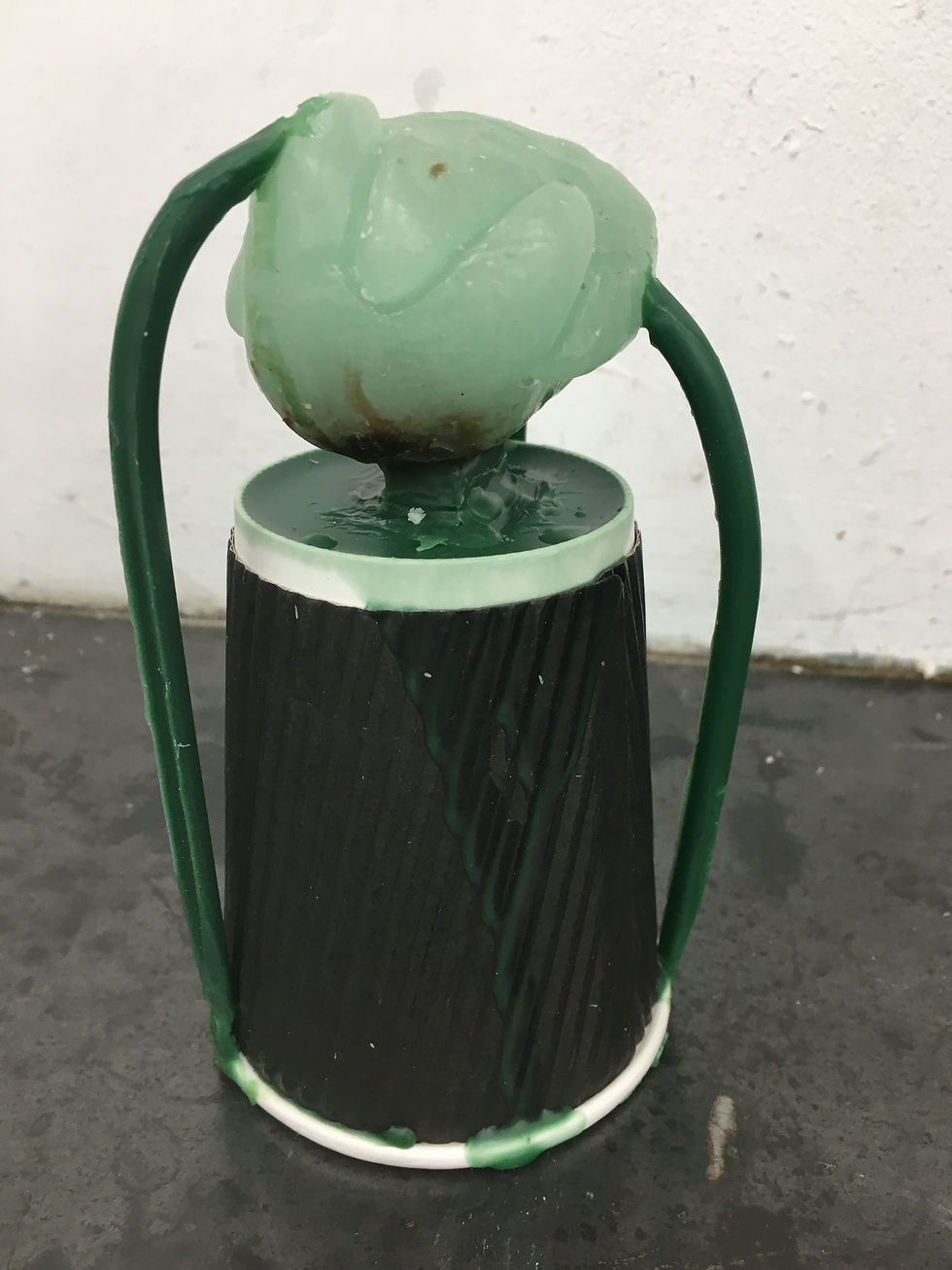
Once all the item is placed upside down and contained within a flask (metal tube container) that is filled with sand to hold everything in place the pour can take place.
Sustainability.
There are many processes involved but also there many of the items that can be re-used.
The clay that is originally used to make the plaster moulds, if looked after and keep in a sealed container, can be used over and over again. I have still got the same bag I bought in Year 1. The wax for the sprues and running up can be used time and time again, if you don't quite get it right and need to adjust things, until it is ready for the pour, you just melt it down in the pan and re-set it. The flasks are constantly used to contain items ready for the pour and even when the finished item is made, if there are any issues and it defects in the process the bronze (or whatever material you use) can be melted down and used again.
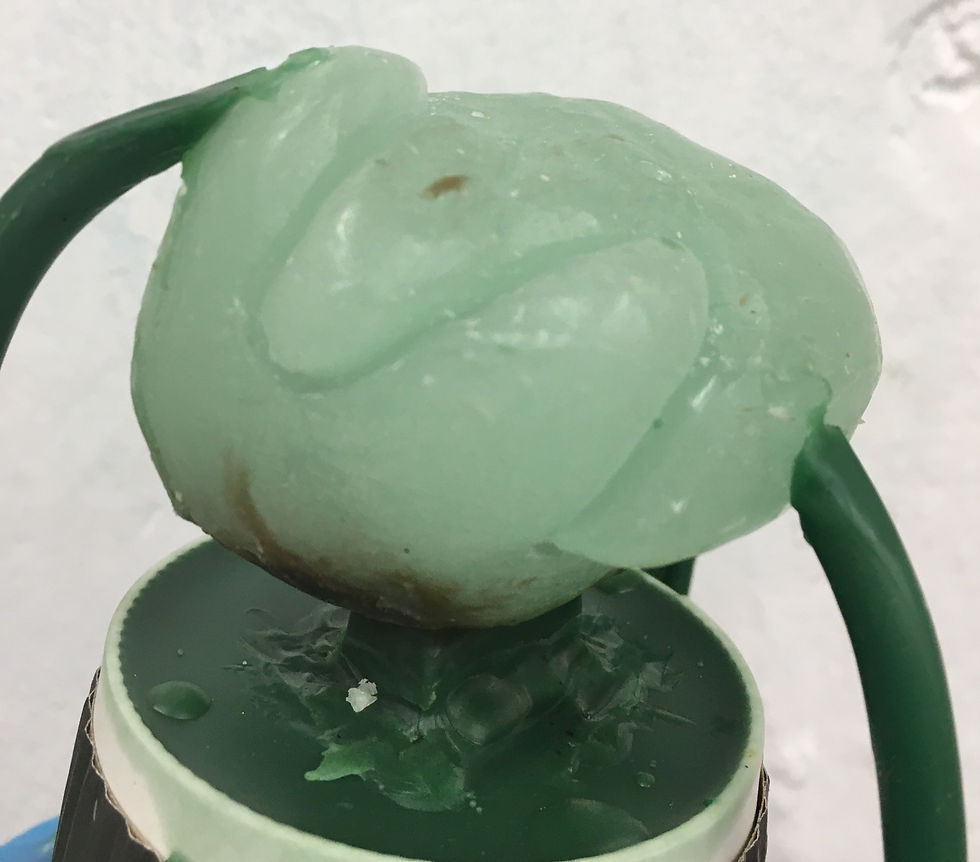
Footnote.... Sadly due to an issue with the kiln and Covid this is just one of many pieces that is probably still sitting in the 3D Workshop three months later... Hopefully it will one day be made into bronze and I can see how it comes out and what finishing it requires.
Comentários