3D Prints.
- carldurban
- Aug 7, 2023
- 4 min read
Updated: Aug 12, 2023
I have eventually started to have my 3D images printed, after a few technical problems with the actual printer. It is quite something to see the object develop, even with all the scaffolding that the printer has to create to support the construction. This particular one is very reminiscent of the 3D image, at this stage little seems to have been lost in the process. The hole on the left side is due to the original item being white and the 3D software struggles with white and reflective objects, this would have had light shining where the hole is and ‘decided’ that there was no information for it to record and therefore print.

This particular object, especially being printed in this blue/grey, although is suggestive of a landscape, it also evocative of a stealth jet fighter. Which considering it comes from the same origin as the finished bronze piece shows how a different material or finish can give a different reading.
I have also played with the scale on all the 3D printed outputs and had them printed as large as I can that the printer is able to. This is possibly 250% larger than the original. This is because I wanted to take it away from a small model or maquette and play with understanding of them all at a new scale. I would have gone larger had the printer been able.

Whereas with the grey print you can clearly see the object developing, with this one it is a lot harder to recognise what the actual finished item will look like. This shape is a very complicated one and although normally the items are printed hollow to print faster and use less polymer, with this one it has to be printed solid. The above image is after four days of printing...
I have decision as this takes some sort of shape as to ho much of it will need to be trimmed off or do I leave it as that is how the printer has translated the 3D image to a solid object. If I modify it by removing a lot of the scaffolding and support work, is that the same as the grinding off the sprues on a bronze cast? Even though these are absolutely necessary in order to create the final cast object. Until it is finished printing I can’t really decide. If it ever finishes printing...
This is an exciting part of the development of this project as it starts to show the next stage in the transformation from random items to instructions to small maquettes, to 3D scans, to 3D prints and then hopefully bronze casts. A lot of processes but also a lot of interpretations by machines and software with little human intervention. I have tried to just let things happen right from the start, with as little interference as possible.
In an excerpt below from Philip K. Dick’s short story about a world where items are brought by humans to be reproduced by ever fading entities ‘Biltongs’ the prints of prints become increasingly useless and less like the original. I just hope that these printers continue to survive and realise my objects, however distant they be from the original. I have limited control over the language and translation.
“The Biltong printing there had grown old and died. Exhausted, he had settled into a silent, unmoving mound of inert matter. The buildings and streets around him, all the things he had printed, had gradually worn out and returned to black ash. “He didn’t spawn,” Charlotte whispered fearfully. “He used himself up printing, and then he just -- died.”
Philip K. Dick. Pay For The Printer (1954) Copyright © (“Satellite”, Oct 1956)

The 3D prints have had varied degrees of success. Two out of three so far have reproduced in a format I would expect from the scans. One in particular has not. This one I would call a failure more of a break down in communication or something that got lost in translation.
There is a lot to unpack with these results and I have the benefit of time to review their present state before taking them further, whether that is to cast them or to develop them in another way.
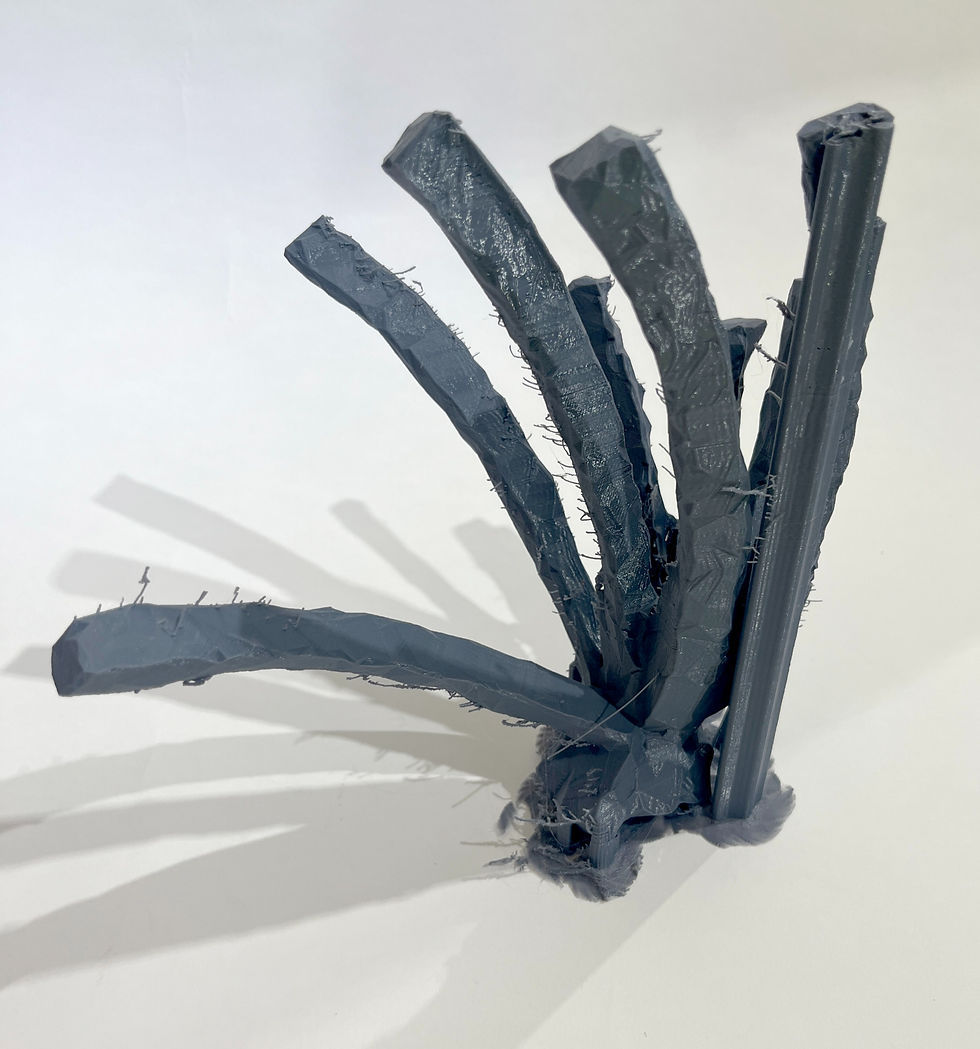
The next one (red) has more scaffolding than item printed and then the printer just gave up after about six days.
It does still have relevance, as by ‘failing’ it has provided me with as much information as if it had printed how intended. I have to look at the outcome and decide whether it is still ‘something’ and if so, what?
There are questions of why? but also questions about acceptance that this is how the printer wanted it to look like, I could not intervene once it had stated to print, it had to run its course.

The three outcomes so far, unadulterated, untouched since printed. One decision is how much do I alter, adjust or modify? As with the bronze cast there are certain parts that needed taking off and cleaning as they were part of the casting process, the supports and scaffolding here are the same, they are added by the process in order to get the completed print.
I also have a further item being printed and it will be interesting to see how this develops through the process. Biggest question is do I stall cast from these or do I look to do something else, or nothing?

Comments